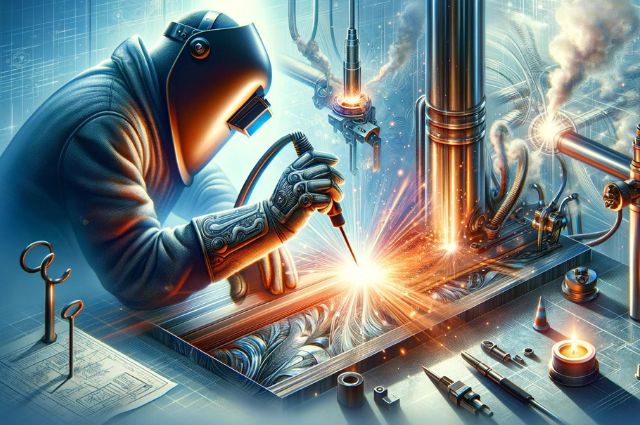
Metal Inert Gas (MIG) welding is a highly efficient and versatile method used in various industries, from automotive manufacturing to home DIY projects. Central to its success is the use of MIG shielding gases. These gases play a crucial role in the quality of the weld produced. They protect the weld area from atmospheric gases such as oxygen, nitrogen, and water vapour, which can cause defects like porosity and spatter. The effectiveness of MIG shielding gas is not only in preventing contamination but also in stabilising the arc during the welding process, ensuring a smooth and consistent weld bead.
Types of Shielding Gases and Their Properties
The most common shielding gases used in MIG welding are Argon, Carbon Dioxide, and mixtures with other gases. Argon is a noble gas, which makes it ideal for welding as it does not react with the metal. It ensures a stable arc and excellent weld quality but can be costly. Carbon Dioxide, on the other hand, is more affordable and provides deeper penetration. However, it can lead to more spatter. Mixed gases often combine both benefits, offering a balance between weld quality, cost, and ease of use. These gases can also influence welding speed and energy consumption, making their selection a key factor in efficient welding operations.
Impact of Shielding Gases on Weld Quality
The choice of shielding gas significantly affects the weld’s appearance, penetration, and mechanical properties. For example, a higher Argon content typically results in a smoother, cleaner weld with less spatter, making it suitable for thin metals and aesthetic applications. In contrast, a mix with a higher percentage of Carbon Dioxide can achieve deeper penetration, which is beneficial for thicker materials. Additionally, the right gas mixture can minimise the risk of weld defects such as cracking or undercutting, enhancing the overall durability and strength of the weld.
Selecting the Right Shielding Gas
Selecting the appropriate shielding gas depends on several factors, including the type of welded material, thickness, welding position, and desired weld properties. For instance, pure Argon is often used for non-ferrous metals like aluminium, while a mix of Argon and Carbon Dioxide is popular for welding mild steel. It’s also important to consider the working environment, as some gases may be less effective or pose safety risks in certain conditions, such as in windy outdoor settings.
Advancements in Shielding Gas Technology
The welding industry continuously evolves, with ongoing research into new shielding gas mixtures that offer improved weld quality, higher efficiency, or lower costs. Recent advancements include gases that reduce environmental impact and specialised mixtures designed for specific applications, such as high-strength steels or metals sensitive to oxidation. These developments enhance the welding process and contribute to sustainable practices, aligning with global efforts to reduce industrial emissions and waste.
Conclusion
Shielding gases are a fundamental component of the MIG welding process. The selection and application of MIG shielding gas have a direct impact on the quality, appearance, and structural integrity of the weld. Understanding the properties and effects of different shielding gases enables welders to make informed choices, leading to better outcomes in their welding projects. These gases not only enhance the welding process but also pave the way for innovation in welding techniques, contributing significantly to advancements in both the quality and sustainability of welding practices. As technology advances, the potential for more efficient, environmentally friendly, and specialised gas mixtures promises to revolutionise the world of welding further.