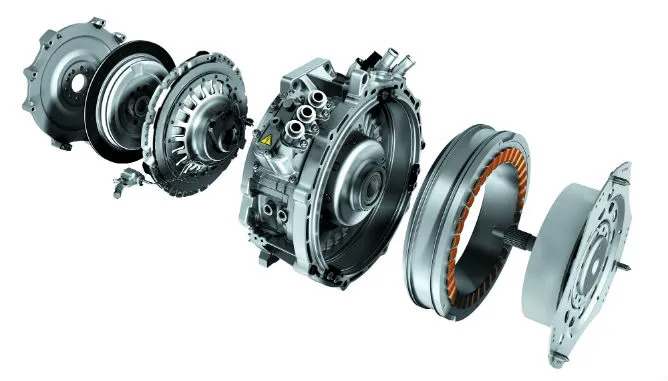
Electric vehicles have revolutionized the automotive industry, with more and more drivers opting for eco-friendly and sustainable options. However, one key component that enables electric vehicles to operate is the motor. Let’s discuss about the different types of motors used in electric vehicles and how they contribute to their performance and efficiency.
Types of Motors Used in Electric Vehicles
1. DC Series Motor
A DC series motor is a type of DC electric motor in which the armature and field windings are connected in series. This means that the same current flows through both the armature and the field windings, producing a strong magnetic field and high torque output.
DC series motors are commonly used in applications where high starting torque is required, such as in electric vehicles, cranes, and hoists. They’re also used in certain industrial applications, such as in printing presses and textile machinery.
One of the key advantages of DC series motors is their high starting torque, which allows them to easily overcome initial resistance and accelerate quickly. They also have a relatively simple design and are easy to control, making them a popular choice in a wide range of applications.
However, DC series motors also have some disadvantages. They can be inefficient at high speeds, and they require regular maintenance to ensure that the brushes and commutator are functioning properly. Additionally, they can be difficult to control at low speeds, which can be a concern in certain applications.
2. Permanent Magnet Synchronous Motor (PMSM)
A Permanent Magnet Synchronous Motor (PMSM) is a type of electric motor that uses permanent magnets on the rotor to generate a magnetic field. The stator windings are arranged in a way that produces a rotating magnetic field. It will interact with the permanent magnets to produce torque and rotation.
PMSMs are commonly used in applications where high efficiency and precision control are important. Such as in electric vehicles, robotics, and industrial machinery. They’re also used in certain renewable energy applications, such as wind turbines and hydroelectric generators.
One of the key advantages of PMSMs is their high efficiency, which can be over 90% in some cases. This is due to the absence of a rotor winding, which eliminates the losses associated with rotor resistance and reduces heat generation. PMSMs also have a high power density and can operate at high speeds, making them suitable for many high-performance applications.
Thus, PMSMs can be more complex and expensive to manufacture than some other types of electric motors. Due to the need for high-quality permanent magnets and precise control electronics. They may also require specialized knowledge and skills to design and operate.
You May Like: How to Apply for Electric Vehicle Subsidy
3. Three-Phase AC Induction Motors
A Three Phase AC Induction Motor is a type of electric motor that uses a rotating magnetic field to induce current and generate torque in the rotor. The motor consists of a stator with three sets of windings, arranged 120 degrees apart, and a rotor with conductive bars or short-circuited windings.
Three-phase AC induction motors are widely used in industrial and commercial applications, such as pumps, fans, compressors, and conveyors, due to their reliability, durability, and low cost. They are also used in many household appliances, such as washing machines and air conditioners.
One of the key advantages of three-phase AC induction motors is their simplicity and robustness. They have no brushes or commutators, which reduces maintenance requirements and eliminates the risk of sparking and arcing. They are also highly efficient, with typical efficiencies of 85-95%. Which can lead to significant energy savings over the long term.
Therefore, three-phase AC induction motors can be more difficult to control than some other types of motors. due to their high starting current and the need for a separate starting circuit or soft starter. They also have a limited speed range and may require additional equipment, such as a variable frequency drive, for precise speed control.
4. Switched Reluctance Motor (SRM)
A Switched Reluctance Motor (SRM) is a type of electric motor that uses the reluctance torque generated by the tendency of a magnetic circuit to align itself with a magnetic field. The motor consists of a rotor with no windings or magnets, and a stator with multiple teeth and windings that are electronically switched on and off to create a rotating magnetic field.
SRMs are commonly used in applications where high efficiency, high torque density, and ruggedness are important, such as in electric vehicles, industrial machinery, and household appliances. They are also used in some renewable energy applications, such as wind turbines.
One of the key advantages of SRMs is their high power density. It can be up to three times higher than that of traditional induction motors. They are also highly efficient, with typical efficiencies of 90-95%. It can operate at high speeds, making them suitable for many high-performance applications.
SRMs can be more complex and expensive to control than some other types of electric motors. Due to the need for precise switching electronics and sensors. They may also require specialized knowledge and skills to design and operate.
5. Brushless DC Motors
Brushless DC motors (BLDC) are more efficient and have a longer lifespan than brushed DC motors. They are also more complex, consisting of a rotor with permanent magnets and a stator with multiple coils. These motors require an electronic controller to regulate the flow of current to the coils, making them more expensive and complex to control.
However, the benefits of BLDC motors include higher torque, better efficiency, and longer lifespan, making them an ideal choice for electric vehicles.
Choosing the Right Motor for Electric Vehicles
When selecting a motor for an electric vehicle, factors such as performance, efficiency, and cost must be taken into account. The type of motor chosen will depend on the specific requirements of the vehicle and the desired performance.
In general, BLDC motors are the preferred choice for electric vehicles, as they offer the best combination of performance, efficiency, and lifespan. However, AC induction motors may be a better choice for larger vehicles or applications that require high torque.
How Electric Vehicle Motors Compare to Gasoline Engines
Electric vehicle motors have a number of advantages over traditional gasoline engines. For one, they’re much more efficient at converting energy into motion, resulting in lower energy consumption and reduced carbon emissions. They also produce less noise and vibration, resulting in a smoother and more comfortable ride.
Another advantage of electric vehicle motors is their instant torque. Unlike gasoline engines, which require time to build up to full power, electric motors can deliver maximum torque instantly. This results in quicker acceleration and better performance overall.
One disadvantage of electric vehicle motors is their limited range. EVs can only travel a certain distance on a single charge. It can be a concern for drivers who frequently travel long distances. However, this issue is being addressed with the development of better battery technology and the construction of more charging stations.
Life Expectancy of Electric Car Motor
The life expectancy of an electric car motor can vary depending on a number of factors. Such as the type of motor, the quality of the components, and the operating conditions.
In general, electric car motors are expected to have a longer lifespan than traditional gasoline engines due to their simpler design and fewer moving parts. The lack of a combustion process also means less wear and tear on the motor components over time.
The most common type of electric car motor is the AC induction motor. It is known for its durability and reliability. These motors can last for hundreds of thousands of miles with proper maintenance and care. The permanent magnet synchronous motor (PMSM) is also commonly used in electric cars and is known for its high efficiency and long lifespan.
However, like any mechanical component, electric car motors can still experience wear and tear over time. Factors such as high operating temperatures, excessive use, and lack of maintenance can all contribute to a shorter lifespan.
To maximize the lifespan of an electric car motor, it is important to follow the manufacturer’s recommended maintenance schedule and avoid harsh driving conditions and extreme temperatures. Regular maintenance tasks such as replacing the air filter, and coolant levels. Also inspecting the drive system can help to ensure the motor is operating at its best.
Overall, the life expectancy of an electric car motor is typically longer than that of a traditional gasoline engine. But the specific lifespan can vary depending on a variety of factors.
Conclusion
Electric vehicles rely on motors to convert electrical energy into mechanical energy, enabling them to operate. While there are different types of motors available, including Brushed DC, Brushless DC, and AC induction motors. The preferred choice for electric vehicles is typically the BLDC motor due to its performance, efficiency, and lifespan.
Read Next Blog:
Which Battery is Used in Electric Vehicle